Link SF34 at Canberra on Nov 10th 2022, propeller strap penetrates cabin in flight
Last Update: May 9, 2024 / 05:12:41 GMT/Zulu time
Incident Facts
Date of incident
Nov 10, 2022
Classification
Accident
Airline
Link Airways
Flight number
VA-633
Departure
Canberra, Australia
Destination
Sydney, Australia
Aircraft Registration
VH-VEQ
Aircraft Type
SAAB 340
ICAO Type Designator
SF34
Australian Federal Police reported three people were assessed for minor injuries.
The ATSB deployed investigators on site and reported a ratchet strap attached to a propeller punctured the side of the plane, with one of its ends appearing inside the cabin shortly after takeoff. The strap had been used to secure the propeller overnight and had not been removed.
The airline reported the aircraft landed safely back, there were no injuries to passengers or crew.
In May 2023 the ATSB released following abstract indicating the investigation is estimated to be finished by Q4/2023:
The aircraft was operating as Virgin Australia flight VA633, scheduled from Canberra to Sydney, New South Wales. Prior to the flight, a strap for retaining the left propeller blade was not removed and the engine was started with the strap attached. The strap was thrown free of the blade during the final stages of take-off and it penetrated the fuselage. One passenger received minor injuries and the aircraft sustained minor damage.
On May 9th 2024 the ATSB released their final report concluding the probable causes were:
Contributing factors
- The aircraft was released for flight with the propeller strap still attached to the left propeller. Parts of the strap assembly subsequently penetrated the fuselage during take-off, injuring one passenger.
- The first officer did not remove the propeller strap as part of the final external check (walk-around) of the aircraft.
- The captain did not notice the propeller strap or the incorrect propeller position prior to engine start.
- The dispatch coordinator did not notice the propeller strap or, during the engine start, the unusual propeller motion.
- On one-third of the Link Airways Saab 340B flights for which video surveillance was examined, including the occurrence flight, the flight crews did not fit the strap extension between the propeller strap and the airstairs. As the cabin door could not be closed with the strap extension in place, its correct fitment would almost certainly prevent a flight from proceeding with a propeller strap fitted. (Safety issue)
- The propeller strap did not have a high-visibility streamer attached, and Link Airways did not effectively manage the condition of propeller straps for its Saab 340B fleet. This affected the visibility of the straps during ground operations. (Safety issue)
- Guidance provided by Link Airways for training of Swissport dispatch coordinators did not explain the appearance, function and importance of the propeller straps. (Safety issue)
Other factors that increased risk
- Swissport did not ensure that the implemented training and audits for Link Airways Saab 340B dispatches incorporated all of the elements required in its Ground operations manual for pre-departure walk-arounds. (Safety issue)
- The cabin manager did not tell the flight crew that an object had penetrated the fuselage. While this had no bearing on the outcome, it limited the information available to the flight crew if aircraft systems had been damaged.
The ATSB analysed:
Pre-flight procedures
The Link Flight crew operating manual (FCOM) required the right seat pilot—the FO in this case— to conduct a final external check (walk-around) of the aircraft before departure. As part of the check, the FCOM required the FO to ‘remove left prop strap and extension and dress the propeller to 45° (the ‘X’ position). In this occurrence, the FO did not see and remove the propeller strap during the final external check, and did not notice that the strap extension was not present at the time. It is likely that the absence of the strap extension contributed to the FO not seeing and removing the propeller strap, since this larger and more obvious strap would serve as a reminder that the propeller strap was still present. Further, the propeller strap streamer was missing, which is specifically designed to attract attention and therefore reduce the chance that someone could miss the presence of the propeller strap (with or without the extension). There was insufficient evidence to determine whether distraction contributed to the FO not seeing or removing the strap.
There was also an opportunity for the flight crew to notice the fact that the propeller strap had not been brought into the flight deck. The FCOM specified that the FO should tell the captain that the propeller strap had been stowed, but it was not done in this instance. If the FO had remembered to confirm strap stowage with the captain, one of the crew members might have noticed its absence. While the FO noted feeling fatigued on the morning of the occurrence, there was insufficient evidence to establish if the pilot was likely experiencing a level of fatigue known to affect performance at the time of the occurrence.
Engine start
During the engine start sequence, there was an opportunity for the captain to notice the propeller strap was still attached prior to start-up. The FCOM required the captain to check the propeller was clear and that the ‘prop tie’ (propeller strap) had been removed. In an interview, the captain recalled checking the left engine area prior to start, but did not notice the strap.
The captain would not have been expecting the strap to still be present, and was probably focusing on ensuring that no people or obstructions were near the propeller rather than the condition of the propeller itself. As discussed in Propeller strap condition, if the propeller strap streamer was present, it would have increased the chance of the captain noticing the strap was still in place.
The captain was not required to check (and did not notice) whether the propeller was in the ‘X’ position or the ‘T’ position, which was used to indicate the presence of the propeller strap. However, sufficiently high winds can rotate an unrestrained propeller to a different orientation prior to engine start, so the propeller orientation would not necessarily alert a pilot to a potential issue.
As part of the engine start, the FCOM required pilots to monitor the instruments for propeller rotation along with other engine instruments. In this occurrence, there was 33 seconds between the propeller moving slightly (indicating engine start) and the cowling pins failing, allowing the propeller to rotate freely. By the time the propeller rotation could be monitored using the instruments (approximately 40 seconds after the start had commenced), the propeller would have been rotating normally. Given that the captain’s attention would have been on the instruments, it is likely that this aspect of the start sequence was not noticeably unusual to the flight crew.
Once the engine start was complete the propeller was likely spinning too fast to see that the propeller strap was still attached to the propeller.
Ground handling and dispatch
The dispatcher did not notice that the propeller strap was still attached to the aircraft during the FO’s final walk-around. The dispatcher was positioned near the cargo bay door during the walkaround, and reported observing the FO moving from the cargo bay door to the airstairs. The dispatcher did not follow the FO during this process, despite it being part of the practical training.
Following the FO or performing a full walk-around in accordance with Swissport procedures (see Swissport dispatcher procedures and training) would have provided a better opportunity for the dispatcher to look for the kind of hazards described in the Ground operations manual (GOM), such as open panels, ‘remove before flight’ streamers and ground service equipment. It should be noted that dispatchers were not trained to look for propeller straps (see Dispatchers not familiar with propeller straps or propeller dressing).
While at the nose of the aircraft for the engine start procedure, the dispatcher did not see the strap when checking the engine was clear. The dispatcher also did not notice the slight movement of the propeller at the beginning of the engine start sequence. In addition to the strap visibility and lack of instruction regarding the strap, the position of the sun behind the aircraft could have limited the dispatcher’s view.
Use of strap extensions
The strap extension was to be fitted between the propeller strap and airstairs, and served to indicate the restricted area around the propeller during boarding. Since it was much larger than the propeller strap, it also served as an additional visual indication that the propeller strap was still fitted. Most critically, the strap extension prevented the cabin door being closed without first removing it from the airstairs.
In this occurrence, being the first flight of the day, the strap extension was not already attached from a previous flight. When leaving the flight deck to begin the line check, the FO did not take the strap extension from behind the flight deck door and attach it between the propeller strap and airstairs following the left engine inspection, as required by the FCOM. If the strap extension had been fitted, the cabin manager (CM) would have been unable to close the cabin door after boarding and the flight would have almost certainly not proceeded without removal of the propeller strap.
An examination of closed-circuit television (CCTV) footage at Canberra Airport showed other Link flights where the strap extension was not fitted prior to departure. Out of 8 observed departures, in addition to the occurrence flight, the strap extension was not fitted twice, including one that was the first flight of the day. It is likely that the differences in aircraft preparation for a first flight of the day compared to a turnaround increased the likelihood of the strap extension not being fitted for departure. As 3 of the 9 Link departures (occurrence flight and 8 previous departures) showed the extension strap not being used during boarding, it is evident that its non-use for the occurrence flight was not an isolated event by a single pilot.
Propeller strap condition
The propeller straps designed and supplied by the aircraft manufacturer included a streamer to aid visibility. However, the propeller strap that was provided for the occurrence aircraft did not have a streamer attached. The presence of a ‘remove before flight’ streamer would have increased the likelihood of the FO, captain and dispatcher noticing the propeller strap prior to departure.
Link’s subsequent investigation found variations in the condition of propeller straps within the Saab 340B fleet. The missing, discoloured or damaged streamers that were still in service would have reduced the likelihood of flight crew and dispatchers seeing and removing these propeller straps. Similarly, the straps with faded or discoloured webbing would have been more difficult to see against black propeller blades. This evidence indicates that the condition of propeller straps within Link’s Saab 340B fleet was not effectively managed, increasing the risk to associated flights.
Dispatchers not familiar with propeller straps or propeller dressing
The training material that Link provided to Swissport for dispatcher training did not include any specific requirements for dispatchers to check for propeller straps or the strap extension. Link’s ground handling manual only noted ‘prop straps’ as an item the flight crew fitted to the cabin door prior to disembarkation. The material did not include any further description of the propeller strap or its function and usage by Link. There was also no information regarding Link’s use of a strap extension, which was used by some operators for Saab 340B aircraft. Consequently, the Swissport trainers (and therefore the dispatchers that were trained) would not necessarily have been familiar with flight crew procedures regarding the propeller strap and strap extension. This would have reduced the effectiveness of dispatchers to notice departures from procedure such as a propeller strap not being removed, or a strap extension not being fitted before boarding.
A trainer thought that the strap extension was permanently connected to the propeller strap. Since the cabin door would not be closeable while the strap extension was connected, it would be reasonable for dispatchers to believe that there was no need for them to look for a propeller strap, since the attached strap extension would prevent the flight from proceeding. Beyond guidance on looking for broad problems like ‘remove before flight’ streamers on the landing gear or flight data sensors, dispatchers would not know to look for attached propeller straps during the dispatch process.
Training material from Link did not mention propeller dressing, or the significance of a propeller in the ‘T’ position (indicating the strap was attached) versus one in the ‘X’ position (free to spin). Training dispatchers to ensure propellers were in the correct orientation would provide an additional, albeit indirect, method of checking for the presence of a propeller strap.
Swissport dispatcher procedures and training
Under the ground handling agreement in place between Swissport and Virgin, and by extension between Swissport and Link, dispatches of Link aircraft were to be carried out in accordance with Link’s instructions. In the absence of such instructions, the agreement stated that Swissport was to ‘apply its own standard practices and procedures.’ Similarly, Swissport’s GOM stated that it applied ‘wherever a client does not have specific procedures relating to the tasks being carried out.’
Link provided Swissport with information for the training of dispatchers to provide ground handling services for Link Saab 340B aircraft. Regarding walk-arounds, there was no detailed procedure provided for dispatchers, although a training checklist provided by Link included the need for a ‘final walk-around’ to ‘confirm … that all doors and other opening[s] are closed flush.’ A Swissport trainer reported they were told by Link staff that walk-arounds were the duty of the flight crew, not the dispatcher. However, the training material provided by Link was for aircraft ramping and dispatch duties, not flight crew duties. The training information provided by Link did not provide any detail relating to propeller straps or their use.
In its investigation report into the occurrence, Swissport stated that a dispatcher walk-around was not required since no standard operating procedure for a dispatcher walk-around had been provided by Link. However, both the Standard ground handling agreement (SGHA) and Swissport’s GOM stated that Swissport’s procedures should be applied in the absence of ‘instructions’ or a ‘specific procedure’ from Link.
If this were to be the case, Swissport’s GOM stated that a walk-around was required for all aircraft dispatches, which was to be a check around the entire aircraft perimeter immediately prior to departure. On the other hand, if Link’s instructions had clearly specified that Swissport staff were not to conduct a walkaround, then complying with this would be consistent with the GOM.
Regardless of obligations under the SGHA, Swissport’s GOM strongly emphasised the need for a dispatcher walk-around, and the walk-around prescribed had more detail than in the training material Link provided. In contrast to Swissport GOM procedures, the training actually given to Swissport ground staff did not require a full-perimeter walkaround, and only required them to observe flight crew moving from the cargo bay door into the cabin, to ensure that doors and hatches were flush with the fuselage, and to ensure that the pogo stick was stowed. CCTV footage from Canberra Airport confirmed that a full-perimeter walk-around was not generally done. Including a complete dispatcher walk-around in the dispatch process would provide a second check that nothing critical has been missed before departure.
It is important to note that in this occurrence, since the GOM did not mention propeller straps, it is not certain that the dispatcher would have noticed the strap if Swissport’s full-walkaround had been implemented.
Audits can be an effective method to detect non-compliance with standard procedures and training. In this case, dispatch audits were conducted by the same Swissport personnel that conducted the dispatcher training. These audits might have been sufficient to prevent dispatchers deviating from the training, but it is not likely that they would detect when the training (and dispatcher actions) deviated from Swissport’s GOM or, more importantly, from the operator’s specific requirements.
Flight crew not informed of fuselage penetration
After realising that an object had penetrated the fuselage, the CM did not inform the flight crew immediately, because this would disrupt the sterile flight deck. Link’s Cabin crew operating manual (CCOM) required cabin crew members to inform flight crew of cabin emergencies as an immediate priority, even with sterile flight deck procedures in place. However, the time between the occurrence (at around the time the aircraft became airborne) and the CM contacting the flight deck (25 seconds after take-off) was not unreasonable, given the unexpected nature of the occurrence, and there being no apparent critical danger requiring an immediate response.
After this, however, the CM spoke to the flight crew several times but did not communicate the nature of the emergency (primarily being an object that had penetrated the fuselage) and this type of information was not sought by the flight crew. This left the flight crew under the impression that the emergency related only to the medical condition of a passenger, rather than the state of the aircraft. In accordance with the CCOM, cabin crew were required to ensure flight crew were made aware of the nature of an emergency or abnormal situation as soon as was practical.
Based on the understanding that a passenger was injured, the flight crew responded quickly and appropriately, returning the aircraft to Canberra Airport. In this case, the flight crew would likely not have done anything differently if they had known more about the nature of the emergency.
However, the CM had no way of knowing whether there was unidentified damage to the propeller or engine, which could be anticipated if the debris is recognised as being from a propeller strap.
The CM also would not have been able to identify damage to other systems, which is a reasonable possibility when any object penetrates the fuselage. If unidentified damage had occurred, the flight crew’s response to any consequential events would have been affected by their assumption that the emergency was not related to the aircraft itself.
Incident Facts
Date of incident
Nov 10, 2022
Classification
Accident
Airline
Link Airways
Flight number
VA-633
Departure
Canberra, Australia
Destination
Sydney, Australia
Aircraft Registration
VH-VEQ
Aircraft Type
SAAB 340
ICAO Type Designator
SF34
This article is published under license from Avherald.com. © of text by Avherald.com.
Article source
You can read 1 more free article without a subscription.
Subscribe now and continue reading without any limits!
Read unlimited articles and receive our daily update briefing. Gain better insights into what is happening in commercial aviation safety.
Send tip
Support AeroInside by sending a small tip amount.
Related articles
Link SF34 at Sydney on Oct 24th 2022, too low of final ILS approach
A Link Airways Saab 340B on behalf of Virgin Australia, registration VH-VEQ performing flight VA-669 from Canberra,AC to Sydney,NS (Australia), was…
Link SF34 at Canberra on Mar 25th 2023, cabin did not pressurize
A Link Airways Saab 340B on behalf of Virgin Australia, registration VH-VEZ performing flight VA-625 from Canberra,AC to Sydney,NS (Australia), was…
Newest articles
France B773 near Beijing on May 13th 2024, cockpit oxygen issue
An Air France Boeing 777-300, registration F-GSQV performing flight AF-293 from Tokyo Haneda (Japan) to Paris Charles de Gaulle (France), was enroute…
PIA B772 enroute on May 17th 2024, hydraulic problems
A PIA Pakistan International Airlines Boeing 777-200, registration AP-BGZ performing flight PK-781 from Islamabad (Pakistan) to Toronto,ON (Canada),…
Subscribe today
Are you researching aviation incidents? Get access to AeroInside Insights, unlimited read access and receive the daily newsletter.
Pick your plan and subscribePartner

A new way to document and demonstrate airworthiness compliance and aircraft value. Find out more.
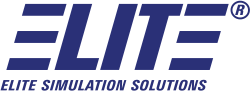
ELITE Simulation Solutions is a leading global provider of Flight Simulation Training Devices, IFR training software as well as flight controls and related services. Find out more.
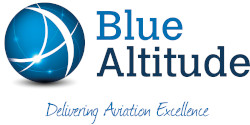
Your regulation partner, specialists in aviation safety and compliance; providing training, auditing, and consultancy services. Find out more.
AeroInside Blog
Popular aircraft
Airbus A320Boeing 737-800
Boeing 737-800 MAX
Popular airlines
American AirlinesUnited
Delta
Air Canada
Lufthansa
British Airways